How mines control driverless trucks

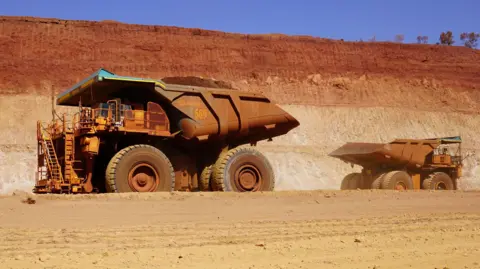
It doesn’t get much further than this. I’m inland in Western Australia, at Rio Tinto’s Greater Nammuldi iron ore mine.
About a two-hour flight north from Perth is an area called the Pilbara.
No one lives here forever. About 400 workers are on site at any one time, and are flown in, working between four and eight days, depending on their shift pattern, before flying home.
Big trucks the size of townhouses, capable of towing 300 tons, make their way through the red earth in various parts of this open pit mine.
For an outsider like me the size of it is intimidating enough, but to replicate that feeling is knowing there is no driver behind the wheel.
During a tour of the area in a full-size company car, one of the trucks appears, coming from the side of the road.
I breathe a sigh of relief as it deftly turns and continues the way we just came. “Did it make you feel uncomfortable?,” asked driver Dwane Pallentine, production superintendent.
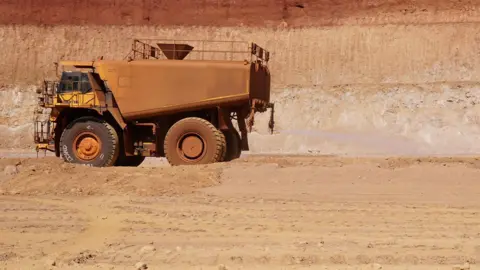
Greater Nammuldi has a fleet of over 50 self-driving trucks that operate independently on pre-defined courses, as well as a number that are always manually driven and operate separately in a different section of the mine.
Also being tested is an independent water truck known as Henry, which, along with the manually operated ones, sprinkles the mine roads to keep the dust down.
My company car is able to work alongside autonomous trucks only because it is equipped with a precise GPS, which allows it to be seen within a virtual system.
Before entering the mine gated area, we entered this system and the controller radioed that we were visible.
Cover our vehicle with a virtual bubble that is “seen” by self-driving trucks and causes them to control their approach by slowing down or stopping as needed.
A touchscreen in our cabin shows all manned and autonomous vehicles and other equipment in the area, as well as “concession lines” that indicate the fastest routes the self-driving trucks intend to take. If I had looked at the screen instead of getting mad I would have seen the truck about to turn.
In addition to all vehicles being equipped with a big red emergency button that can stop the system, autonomous trucks have lasers and radars in the front and rear to detect collision hazards.
The senses also find obstacles. If a large rock fell from the back of the truck, the sensors on the next truck could detect it and the vehicle would stop.
However, some trucks seem to be more sensitive – on my journey I see a couple that have been hampered by bad roads.
Coordinating and monitoring these robots is Rio Tinto’s Operations Center (OC) in Perth, about 1,500km (930 miles) to the south.
It is the arterial center for all of the company’s Pilbara iron ore operations, which include 17 mines in total, including the three that make up Greater Nammuldi.
Directed from here by regulators, include more than 360 self-driving trucks at all sites (about 84% of the total fleet is automated); a network of highly private long-distance trains to transport mined ore to port facilities; and about 40 independent drills. OC personnel also remotely manage plant and port operations.
Autonomy is not new to Rio’s Pilbara operations: the introduction began in the late 2000s.
And it’s no exception: Australia has the largest number of private trucks and other mining equipment of any country, and some mining companies in the Pilbara are also using the technology.
But the scale Rio has grown its operations to here, including Greater Nammuldi – which has one of the largest private truck fleets in the world – gives it global significance.
And it is a global trend. According to GlobalData the number of self-driving trucks worldwide has quadrupled in the past four years to more than 2,000, and most are made by Caterpillar or Komatsu.
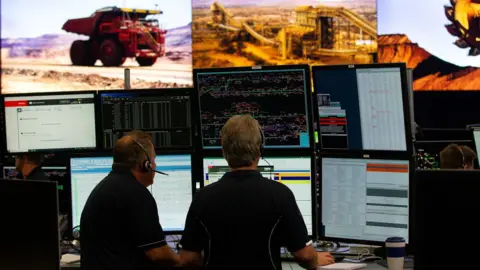
The main reason for introducing this technology was to improve the physical safety of workers, said Matthew Holcz, managing director of the company’s Pilbara mines.
Mining is a dangerous job: heavy equipment can be used unexpectedly by people who may tire. “The data clearly shows that, through automation, we have a much safer business,” said Mr. Holcz.
It also improved productivity – up to 15%, he estimates. Standalone machines can be used more because there are no gaps due to shift changes or breaks. And private trucks can also move faster if there are less manned equipment on the scene.
Such automation is not cheap. Rio won’t disclose how much it has spent on its Pilbara automation project so far, but observers put it in the multi-million dollar range.
Meanwhile, job opportunities have changed. Narrative could be one of robots taking over jobs, but that doesn’t seem to be the case here so far.
Although OC has almost one operator for every 25 autonomous trucks – according to Rio, no one has lost their job due to automation.
Instead, there was a redeployment: truck drivers joined the OC as controllers themselves, were given re-skills to operate different pieces of equipment, such as excavators, loaders and dozers, or to drive manual trucks in different areas.
On the OC’s large open-plan floor, among banks of monitors arranged in clusters of different mines, I meet Jess Cowie, who used to be a hand driller but now directs the independents in the central drill pod. “I still put holes in the ground…without the dust, noise and being away from my family,” he said.
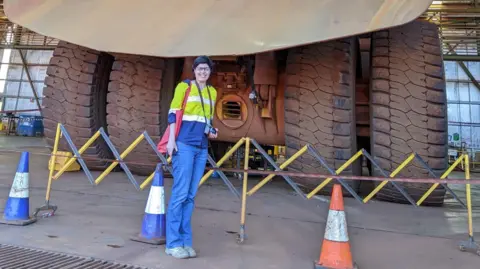
Automation is bringing a “step change” in terms of safety in the mining industry says Robin Burgess-Limerick, a professor at the University of Queensland in Brisbane who studies human factors in mining. But it doesn’t mean there isn’t room for improvement.
Professor Burgess-Limerick analyzed incidents involving autonomous vehicles reported to regulators.
As he sees it, the interfaces used by workers both in the field and in control centers to access information are poorly designed. There have been cases where field workers have lost situational awareness, which a better screen design could have prevented. “Technical designers should put more effort into thinking about people,” he said.
And there’s a risk that the workload of administrators can be overwhelming – it’s busy, high-level work.
Overconfidence, where people are so confident that autonomous machines will stop that they start putting themselves at risk, can also be a problem, and he notes that effort should be directed at improving the trucks’ own ability to detect moisture. There have been incidents where wet roads have caused them to be unable to tow.
There could be legitimate safety concerns about autonomous machines, said Shane Roulstone, coordinator of the Western Mine Workers Alliance, which represents mining-related workers in the Pilbara.
He points to a terrible incident in May when a private train hit a broken down train from behind, the workers who were repairing it in front (they got out before it hit but were left shaken).
But Mr Roulstone also praised Rio more generally for having, over time, developed “good strategies, processes and policies” around how people interact with self-driving cars.
Mr Roulstone expects that at some point redeployment options will be reduced and there will be job losses. He says: “The statistics are just there.
Meanwhile, Rio’s automated journey to the Pilbara continues with more trucks, drills and Henry the water tanker. It also looks closely at Komatsu and Caterpillar’s work to develop unmanned excavators, loaders and dozers.
In the afternoon, while waiting at the Greater Nammuldi Airport for the last flight back to Perth, the announcement came that it had been canceled due to a problem with the plane. That’s 150 more people who will now need to be fed and housed. It’s not a Rio thing, but I can’t help but think that we humans are complicated compared to robots.
Source link