The amazing way the potato industry has reduced its emissions

Inside the sprawling PepsiCo factory in the Netherlands that makes more than a million sacks of potatoes every day, almost all of the plant’s greenhouse gas emissions come from one step: frying the chips. The process has been running on a gas boiler. But soon the factory will open a new system that can use renewable electricity instead.
The technology, from a German startup called Kraftblock, uses a shipping container filled with tiny spheres designed to absorb heat. If there is plenty of cheap solar or wind power available on the grid, the system charges by using electricity to heat the material in the container. It can store heat for a few minutes or as long as two weeks, releasing it when needed when the factory needs it.
At the PepsiCo plant, the new standard technology will be rolled out in stages. First, technology can reduce emissions in half. A complete switch to gas can eliminate 98% of emissions—about 17,000 tons of CO2 per year.
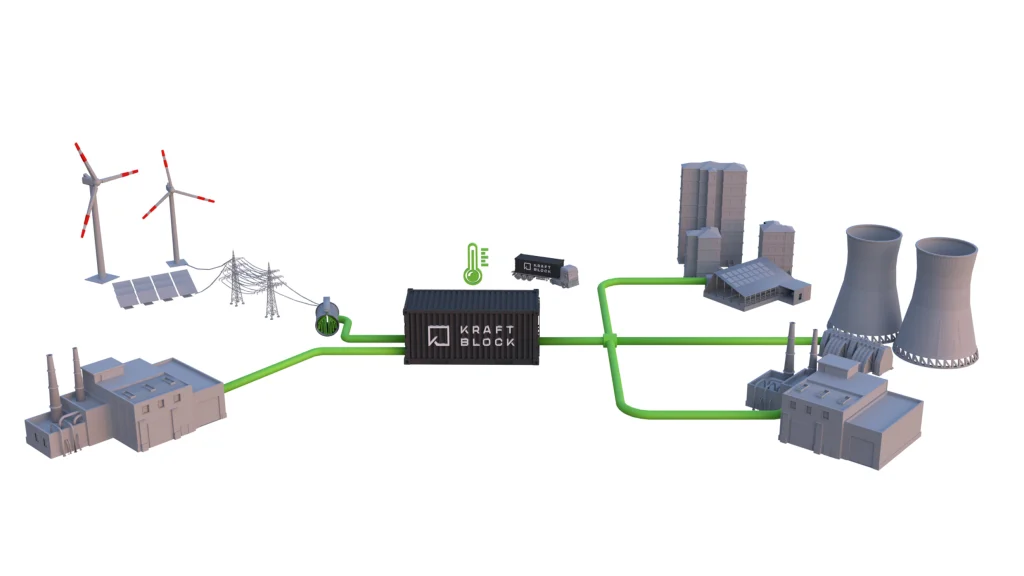
The same technology can be used in any type of industry, from a steel mill to a brewery to a chemical plant. Industrial heat is a major climate polluter, accounting for about 20% of global emissions. “For us, it was not easy to say that, if we can eliminate carbon emissions, we can take a big step in the fight against climate change because we will significantly reduce carbon dioxide emissions,” said Kraftblock founder and CEO Martin. Schichtel.
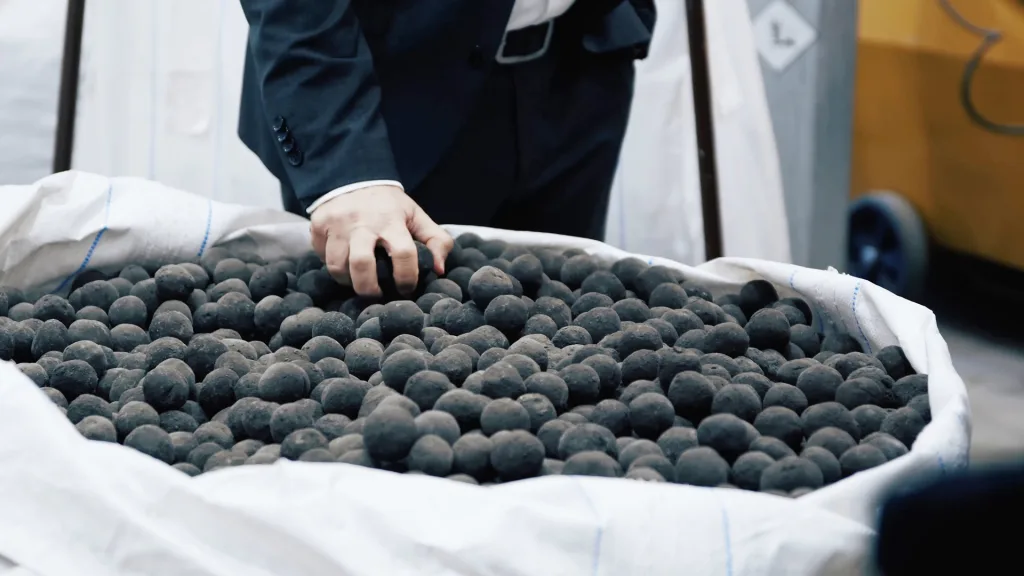
In the past, it was difficult for manufacturers to switch to renewable energy. Industries need a continuous source of energy (a chip factory runs 24/7, for example) and the sun and wind are only available at certain times. Factories are often built around fossil fuel-powered machines. And the very high temperatures required for some industrial processes can’t work well on gas.
But Kraftblock technology can provide continuous heat, fit existing appliances, and provide heat up to 2,500 degrees Fahrenheit. Operating costs are competitive with gas, Schichtel said. And industries can recover the cost of the initial investment within a few years.
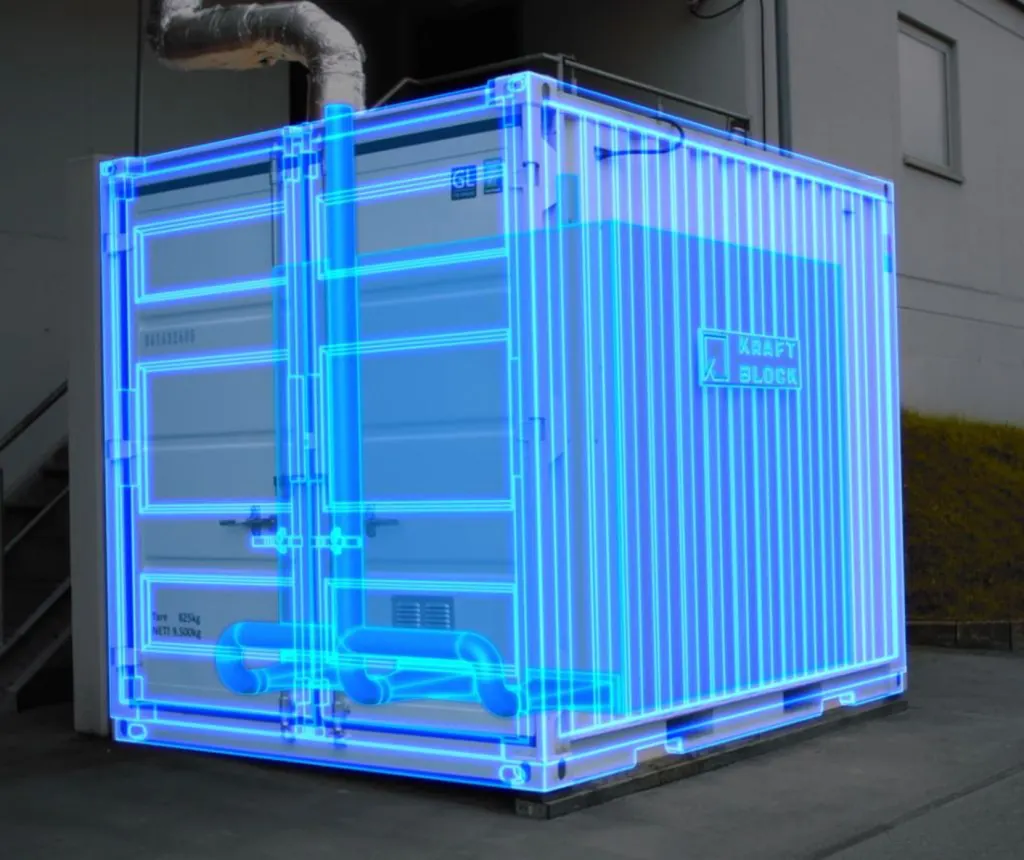
In another project, the company is using waste heat from a ceramics factory to recharge the plant’s storage system. Because its technology can provide more accurate heat than the gas system the industry previously used, the quality of pottery is also improving—and the industry has to throw away less waste. Kraftblock installs systems in many other factories, including steel mills in India.
Startups like Antora Energy and Rondo Energy have developed similar technology, using large “bricks” to store heat. Kraftblock’s design is a bit different, Schichtel says: The round shape of its design provides more surface area, so it can absorb and release heat more quickly. The “pellets” can be made in different sizes (in the Pepsi factory, slightly smaller than golf balls) depending on how the factory will use the heat. Each pellet is made from recycled materials such as steel slag that is ground into powder and combined with a proprietary binder.
The company produces the technology in Germany, but is also starting to work with partners around the world to license and produce it themselves. “That means we can scale quickly,” Schichtel said. The challenge of changing energy sources is huge: China alone has more than 6 million producers.
Source link